PART I
Corps of Engineers
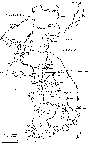
Map of Korea (19K)
1. Three River Crossings
Capt. Richard P. Lepke, 3d Engineer Combat Battalion
The 3d Engineer Combat Battalion (24th Infantry Division) was in a rest area at Kyongsan on 17 September 1950, after a series of long moves and fights around the Naktong perimeter. I commanded Charlie Company. At 2300 the battalion staff and company commanders were summoned by the battalion commander (Lt.Col. Peter C. Hyzer). He told us that we were to make a series of assault crossings of the Naktong River, carrying the entire 24th Infantry Division. The operation was to jump off at 0245, 19 September 1950, south of Waegwan and northwest of Taegu.
Able and Charlie Companies were to get the tough jobs of carrying the two assault regiments of the 24th Division. Able would carry the 19th Infantry, while Charlie was responsible for the crossing of the 21st Infantry. The regiments would cross the Naktong simultaneously, some six miles apart.
At the time of this meeting, not even the battalion commander had had a chance to make a reconnaissance or examine aerial photos of the crossing area, even though the operation was to begin in twenty-seven hours. The battalion had no assault boats but we were promised these at the crossing site by corps engineers. Further, we were to receive one boat per company on the following day in order to familiarize the men with the equipment.
After days before this order was issued we had received a hundred Koreans for each company as replacements. We had started a training program for them but we had not made much progress because of our constant preoccupation with combat. We had a language barrier and all communication was channeled through their interpreters and through one of our NCOs who spoke fluent Korean. The infantry regiments also had Korean filler personnel.
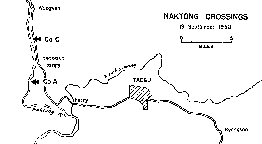
Naktong Crossings 19 September 1950 (9K)
None of the engineers had received any assault training in Korea, and many of the people who had had practice in Japan were now casualties. Probably not over ten per cent of the U.S. personnel had launched an assault boat since their days of basic training. The infantry was also without assault river-crossing experience. There wasn't time for much coordination between the engineers and the infantry. To top it all, our Korean replacements had never before seen an assault boat.
The next day (18 September), while the engineers were familiarizing themselves with the one boat per company, the company commanders and key officers of the battalion staff joined the infantry in a reconnaissance of the Naktong. Our reconnaissance party was much too large, involving six jeeps and twenty persons. Near the river bank we came under enemy observation and received some rounds of mortar fire. No one was injured.
The engineer battalion was bivouacked twenty-five miles from the proposed crossing sites. The route to the crossing sites crossed the Kumho River, but all of the bridges had been blown. An underwater (sandbag) bridge had been operated by the North Korean Army and was being used by the U.S. troops, but this would not handle light vehicles because of the depth of the water. All jeeps had to be carried on a small ferry.
As we returned from our reconnaissance we found traffic backed up for a couple of miles, bumper to bumper, east of the ferry. The road was only one and a half lanes wide and the heavier vehicles were unable to move to the underwater bridge until the jeeps, which were mixed in the column, moved onto the ferry. These were 24th Division vehicles moving up for the crossing mixed with vehicles of corps engineers (repairing the underwater bridge), and a scattering of trucks from other units.
When I returned from my reconnaissance at 1700, I found Charlie Company loaded and ready to go. Attached to us for this crossing were a platoon from Baker and one from Dog. Since we had only our organic personnel and equipment, and carried no assault boats to reveal our intentions, we were allowed to move during daylight. We moved independently of battalion.
There was no traffic control but we moved normally until we approached the ferry. Then we had to move slowly and lost a full hour. Still we reached our initial assembly area south of Naksan-dong by 1930.
I left Charlie Company in defilade and moved forward to the crossing site with the two platoon leaders who were each to be responsible for moving an assault infantry company. We planned to cross the two companies abreast, about a hundred yards apart. I showed the lieutenants their sites, found an abandoned foxhole near the river bank which I claimed as my forward CP, then returned alone to the company.
I had to infiltrate the company out of the initial assembly area, for it was not quite dark and enemy mortar fire was being concentrated on one flat stretch of the road. We closed unharmed in our forward assembly area at 2100. It was an apple orchard just three hundred yards behind the crossing sites. A prominent house nearby came to be a favorite target for artillery fire next day.
The Naktong River at this point was some four hundred feet wide, and had a moderate current. The river bank at one site was a sheer drop of some seven feet. This was cut down by the 2d Platoon after dark. At the second crossing point the bank was cut by a path which led to the beach. From the bank to the water's edge ran a flat, sandy beach about a hundred yards wide, punctuated only by some abandoned tactical wire. The beach was not strong enough to hold vehicles.
I assigned the 1st Platoon to the first crossing site, the 2d Platoon to the second site. The 3d Platoon was to unload the boats when they arrived and to organize the infantry into boat crews. To the attached Baker Company platoon I gave the job of laying a pierced-plank roadway (of airstrip type) over the beach as soon as the first wave was landed. This would facilitate jeep-ambulance and ammunition traffic. The attached Dog Company platoon was to stand by to await orders.
The infantry started arriving in the final assembly area at 2300 and closed in the area by 0100. We had plenty of time to break them down into boat crews and give them elementary instructions since the assault boats still had not arrived.
The commander of the infantry regiment was much upset over the delay, but there was nothing we could do. I saw him talking to Colonel Hyzer several times and I know that messengers were sent out to try to locate the missing boats. At one time the regimental commander mentioned calling off the attack, as it did not appear that the crossing could be made during darkness.
Finally, at 0400, the twenty-eight assault boats arrived. They were loaded both on pole-type trailers and in the beds of 2-1/2-ton trucks. It is hard to unload an assault boat from the bed of a truck, and this slowed down the operation. Worse, however, the drivers simply disappeared as soon as the trucks halted. We had to locate our own drivers to spot the trucks and trailers.
After all twenty-eight boats and their engineer crews were lined UD along the road near the river bank, the infantry came forward. Daybreak came as the first wave was on the water. There was no enemy fire at first, but as our boats reached the center of the stream an extremely heavy volume of small-arms fire hit them. Mortar and SP fire began to strike the near bank and the assembly area.
Apparently our simple instructions had not been understood by the Korean infantrymen, for they refused to leave the boats, and a few returned to the near shore. Sergeant Weird broke his carbine over the hand of one man to get him to release his hold on the guide rail.
As soon as the infantry landed on the far shore, the boats immediately started back. Eight of the twenty-eight assault boats did not make it back. In some cases the current carried them too far downstream and the inexperienced paddlers could not return them. In others, the boats were so riddled that they sank and their engineer crews returned in other boats. Of the Korean engineers who went with the first wave, none was known to return. Maybe they misunderstood their mission and stayed with the infantry. Maybe they drowned-we had no life jackets. Later, when we tried to round up all of our Koreans for replacements, we could locate only 22 of our original 100. Many had just conveniently disappeared for a short time, however.
As the returning boats reached the near shore, the enemy turned his fire on the second wave as it moved by to the beach. These infantrymen took cover on the beach by Iying on their bellies near the water's edge until Sergeant Weird called for them to get loaded and help their buddies on the other side. Hearing this, one sergeant jumped up and yelled, "If the engineers can stand up and take it, so can we!" To a man the infantry hurried to the water's edge and loaded up.
As soon as we counted our boat losses we sent an urgent request to battalion for replacements. In an hour we received sixteen. We also got a boat-repair detachment which was attached to battalion for this operation-but these men claimed they had no equipment with which to make repairs. Only their sergeant would leave the cover of the orchard and go onto the beach to survey our damaged equipment.
The fire on the near beach made it impossible for the platoon of Baker Company to lay its roadway. Some self-propelled guns kept firing on our assembly area and beach until 0930.
The infantry on the far shore reorganized quickly but had strong resistance from the enemy. Our artillery helped and so did the Air Force. When the planes began to use napalm some of the North Koreans panicked and ran. These were immediately shot like quail.
The fighting on the far shore lasted about thirty minutes. The infantry carried air-identification panels on their backs and we could see little envelopments and assaults taking place. Our men were aggressive and moved right up to the enemy without hesitation. Soon we watched the panels moving up the draws, over the crest, and out of sight.
We kept crossing the infantry into the afternoon. By this time we had crossed two battalions of the 21st Infantry and were working on the third. The crossings had cost my company 42 men, only 8 of whom were U.S. troops. What happened to these men I don't know, since we had no time to locate the missing after the operation was over.
At noon, while we were still paddling the 21st Infantry across the Naktong, I was alerted for another crossing. Charlie Company was selected to cross the Naktong again that very evening, this time carrying the 5th Infantry above Waegwan. We were selected because we were the only company in the battalion assembled at one nearby site. Dog Company was to take over our present operation and support the 21st Infantry on the far shore.
I took my executive officer and a sergeant with me on a reconnaissance. We joined Colonel Hyzer and some of his staff officers, and proceeded to Waegwan where we met the commander of the infantry regiment (Colonel Throckmorton). Colonel Throckmorton told us that his regiment was clearing the bank of the Naktong as far north as Hill 303, where he was to make a juncture with friendly troops. Hill 303 was the key to the operation because of its commanding height, but it had not yet been taken. In any case, it would be necessary to cross at least one battalion that night, even if the east bank were not cleared of the enemy.
The attack was parallel to the river bank and Hill 303 was some ten miles north of Waegwan. I was given leeway to select the crossing site anywhere in this ten-mile zone. I moved my small party to the rear of the lead company of the 5th Infantry. We had to hit the ditch several times when the enemy put up small bits of resistance.
At 1430 the infantry still had not reached Hill 303, so I decided that to get a daylight reconnaissance I would have to select a crossing site somewhere between my present location and Waegwan. Two miles north of town I found a site where the banks, turnaround, assembly areas, approaches, and the far shore looked pretty good. By radio I ordered the company to meet me on the road, and I started back to Waegwan.
In Waegwan I learned that the 21st Infantry, which we had crossed that morning, was moving along the far shore of the Naktong. This meant we could make an administrative crossing. I inspected a blown out bridge in Waegwan and decided this would be a good site. Charlie Company reached town almost as soon as I did, and the boats were delivered to us by corps engineers within another thirty minutes. By 1700 or 1730 we began to land the infantry on the far shore. We improvised a ferry and began moving men, jeeps, and equipment on it. We had one battalion across within forty-five minutes.
Our company kitchen was set up in an orchard in Waegwan and we fed the men in shifts. But before I got a chance to eat, I was ordered to cross the other two battalions of the 5th Infantry eight miles north of Waegwan near Hill 303, which we now held. I moved out to make a reconnaissance before it became completely dark.
We selected a site, but as the infantry seemed in no hurry to cross, we held off until the following morning (the 20th). We continued to operate the ferry at Waegwan all night of 19-20 September and left one platoon in Waegwan for that purpose. The other two platoons moved up to the new site.
In the crossing the next morning our site was defiladed, we had infantry on both flanks to give covering fire, mortars were emplaced, tanks and self-propelled guns were registered, and the air support was excellent. The Air Force bombed and strafed a village near the crossing site and maintained armed reconnaissance overhead. The crossing was unopposed.
We crossed two battalions before noon and I loaded my men to move on. I reported to battalion in Waegwan-hopeful that we could get a rest. Instead we were ordered to support the 19th Infantry in an attack on Sangju. We gave general engineer support in this operation. The encounter was brief because the enemy was surprised by the flanking attacks our river crossings made possible.
Within three days Charlie Company had received orders for, had planned, and had executed three river crossings, supporting two different regiments. During the same period it had given general engineer support to a third regiment in attack.
In the crossing of the Roer River in Germany, my engineer battalion had three months of preparation.] We actually formed the exact crews and carried the same groups of infantry in dry-run crossings of a similar river under similar conditions. How different was Korea!
1. I then commanded the 2d Platoon of Company B, 121st Engineer Combat Battalion (29th Infantry Division).
2. Improvised Bridge
Capt. Richard F. McAdoo, 65th Engineer Combat Battalion
In Korea, improvising was the normal thing in bridge construction. With minefields, explosives, or fortifications we could follow doctrine closely. But bridging was different.
We usually didn't have the required materials for any job, and we never had an engineer dump close at hand. In the first six months of Korea, lack of reinforcing engineer units meant that we had to rely on our own resources. When the division needed a bridge it was up to us to build it, make it class 50 if possible, and see that it was built to last.
How important bridge construction was to a combat engineer company can be realized by looking at the record of Company A, 65th Engineer Combat Battalion-thirty-five bridges built in nine months. We built eight timber bridges, three from 120 to 180 feet long, in one week! The Nam River crossing at Chinju was typical of the improvising we had to do to accomplish our mission.
From 16 to 26 September 1950, the 25th Infantry Division made its drive out of the Pusan perimeter and captured Chinju. The 35th Infantry, with Company A, 65th Engineer Combat Battalion, attached, spearheaded the attack. Three days before we reached Chinju, the commander of the 35th Infantry (Col. Henry G. Fisher) asked me what plans had been made to bridge the Nam River. I didn't know and I had trouble getting telephone contact with battalion to find out. Even after I got to talk with the battalion executive officer, I didn't get an immediate answer. He had to call me back, and gave me the message for the engineers (and, incidentally, the infantry): "Don't worry about the Nam River. The division will halt at Chinju." But when we reached the river, the division's plans were changed and we were ordered to cross and continue the attack.
Company A worked with the infantry in the assault crossing of the river. The enemy had only a few squads of men on the far shore and they pulled out after a very short skirmish. The infantry had a few casualties; we had none. Immediately after this we began to build a bridge.
At Chinju there was a high-level concrete bridge which had been partially destroyed. We couldn't repair it because the bridge was too high and the destroyed spans were much too long. Unfortunately, we didn't have the materials to make a new bridge, either.
The Nam River at this point was 300 feet wide and about 6 feet deep, and the current was swift. Downstream from the main highway was a fordable site for tracked vehicles. We helped to cross a battalion task force of the 35th Infantry by towing the wheeled vehicles with tanks and a D7 dozer. My 3d Platoon moved out with this task force and I had only the remaining two platoons to bridge the river.
At 1600 we faced our first problem: locating materials. We had 7 pole-trailer loads of various-sized timbers, 2 truckloads of 3-inch-by-12inch decking-and that was all. We sent reconnaissance parties out to find anything that would help. First we found 15 steel sections commonly used as sheet piling, each 50 feet long. These were in the stream bed and apparently had been discarded when the permanent bridge had been built. In addition to these, about two miles from the bridge site we located a large stockpile of heavy timbers suitable for bridging. These timbers were a better building material than the steel piles, but the narrow road from the bridge site to the timbers was bumper to bumper with trucks waiting to cross the river. The assistant division commander stayed at the bridge site giving us priority on the roads and all the help he could, but the trucks going two miles and back to load timbers took six hours for the round trip. Five of these hours were lost because of the congestion.
To speed the project we pulled the steel piles out of the river and used them. When darkness came we took a chance and used truck headlights for illumination. In spite of the fact that the enemy had been pushed off the far bank only the afternoon before, we had no interference.
The stream bed was of sand, and we knew that we could not build a lasting bridge in that strong current without spending a great deal of time making strong footings. But in this project speed was more important than permanence. We just placed 12-inch-by-12-inch timbers, 14 feet long, drift-pinned together on top of one another, to form intermediate supports. The bridge was at water level, which made it easy to float the supports out to position, set them vertically, and attach the stringers. For the first three spans we used the steel piles as stringers on 40-foot centers. The remaining stringers were made with 6-inch-by-12inch or 12-inch-by-12-inch timbers, and varied from 15 to 20 feet in length.
We had 140 pieces of decking material-only twenty per cent of the requirement for this bridge-and we found no other suitable material nearby. We determined that this was enough, however, to build two treads. One would be 2 feet wide, the other 3. We spaced the treads so that a jeep could use them-but it would have only 2 inches of leeway on the inside of each tread. Our 2-~/2- ton trucks had no difficulty crossing, but wide ammunition trailers could just cross without going off on the outsides of the treads. We placed small curbings to prevent accidents. The capacity of this bridge was estimated at twenty tons.
While the engineers worked on the bridge, five hundred civilians helped on the approaches. Here we had a problem of fill and had to use rubble and everything else available for the job. We took fifteen mines out of the path of the far approach.
Traffic was moving down the approaches and across the bridge within twenty hours of our starting time. We spaced the vehicles fifty feet apart and watched the structure very closely. It was both fearful and wonderful to watch the give in those steel-pile stringers.
Soon after traffic started, Company A moved out with the 35th Infantry. Company C's men took over the maintenance and completion of our bridge. They immediately started to sandbag the base of the intermediate supports, for without footings the current had already begun to suck the sand out from under them. Company C even put in additional intermediate bracings-while traffic was moving over the bridge.
This expedient bridge lasted as long as it was maintained, and until the old bridge was repaired. I believe this was ten days or so. I wouldn't recommend this as a model structure, but it did put the division across the Nam River fast.
3. Causeway at Osan
Lt. Sam D. Starobin, S2, 65th Engineer Combat Battalion
During the withdrawal of November 1950-January 1951, the 25th Infantry Division withdrew across the Han River at Seoul and continued south on the main road as far as Chonan. At Osan we crossed the Chinwi River and there the 65th Engineer Combat Battalion blew the bridge. We believed we were withdrawing from Korea and we did thorough work on our demolitions.
The bridge at Osan was a 28-foot, two-lane, four-span, concrete structure. The abutments were fifteen feet high. The bridge was demolished by blowing alternate piers and the south abutment. This left a saw-toothed appearance.
Four weeks after we had destroyed this bridge we were back to it and were faced with the problem of crossing the Chinwi River. Osan was built up to the bank of the river, which prevented us from building a bypass alongside the bridge. We had to go east of the town with a detour, then ford the river upstream.
Our new bypass was not satisfactory. It lengthened the route by more than a mile and the river bed gave us a great deal of trouble. The spongy clay was frozen several inches deep, but the constant movement of our heavy vehicles over it soon broke this crust and the vehicles bogged down. We had to move the bypass several times.
We did not feel justified in expending materials or labor to make this bypass permanent and we feared high water would make it useless. We didn't have 280 feet of bridging, and a shorter bridge would have to cross the spongy river bed.
The battalion S3 (Major Joseph Pessa), the CO of Company A (Capt. Richard F. McAdoo) and I held a conference at the bridge site. We concluded it would be more practical to build a new bridge than to repair the damaged one. But we also found that the deck of the old concrete bridge was adequate for a causeway.
Company A placed four hundred pounds of TNT kicker charge to blow piers 1 and 3, and the north abutment. The explosions were simultaneous.
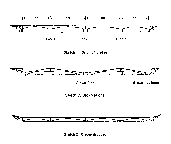
Bridge Sketches (10K)
After the site cleared we could see that our calculations were accurate and that the bridge had dropped as planned. The concrete deck of the old bridge now formed a causeway over the banks and stream some four feet above the ground. There was plenty of room underneath for the river to flow at low stage.
Within six hours of our conference traffic was rolling across the newcauseway. There was no limit on tonnage on this structure, but it was limited to one-lane traffic.
During the heavy spring rains several other bridges along the route were washed out. I know that this one was functioning perfectly as late as April. The river might have gone over it later, but it could never be washed away.
We used this system of stream crossing several times later. It always worked.
4. Last of the Han Bridges
Capt. D. J. Haden, Lt. Rodman M. Davis, Lt. Jack R. Wheatley, Company C; Capt. Donald E. Roush, S4, 14th Engineer Combat Battalion. (Interview by Capt. B. C. Mossman, 6th Historical Detachment.)
On 15 December 1950, the 14th Engineer Combat Battalion, supporting I Corps, was ordered to assume responsibility for the security and maintenance of the floating M2 and M4-M4A2 bridges over the Han River at Seoul. The battalion was further ordered to prepare plans for removal and for demolition of each of these bridges.
The big maintenance problem was to keep the ice broken up around the floating bridges. Ice was a particular problem because the Han River is tidal. Instead of freezing smooth, the ice froze in waves that were constantly building up on the pontons and between them. The four- to five-inch-thick ice alongside the bridges had to be chopped up-and broken by driving DUKWs over it. Ice patrols were sent along the river to report large floes.
The order to dismantle the M2 bridge on 2 January 1951 was received on 1 January. Company C was ordered to do the dismantling, assisted by a platoon of Company B, and trucks and cranes of the 55th Engineer Treadway Bridge Company.
One detail planned to take down the north and south bank trestles, one squad working at each. A second detail would disassemble the bridge into four-float rafts. A squad would work on each raft and move it to one of the thirteen disassembly sites, located downstream of the bridge on the south bank. One platoon was to operate the ponton deflation point, established near the disassembly points.
The weather on 2 January was cold and windy; the temperature was near 10 degrees. The cold made it difficult for the men dismantling the bridge, but did not hinder the work noticeably. The day was so bright that the glare from the ice was hard on the eyes.
Dismantling the M2 bridge took eleven hours. The men detailed to the job reported at the bridge site at 0530 to break the ice, and began actual disassembly at 0700. The trestles and ponton sections at each bank were first lifted, and the bridge was then broken down into fourfloat rafts. Once a four-float raft was removed from the bridge, a DUKW towed it to one of the disassembly sites for further dismantling. The DUKWs were needed because some of the damaged floats had become filled with water and ice, and were too heavy to tow by hand.
At the disassembly site, each four-float raft was broken down into separate floats. Ice had collected in front of the rafts as they were towed, and they could not be brought close enough to the bank to be walked out. Cranes were used to lift them.
The removal of pins between the sections was a serious problem. Some of the pins had rusted; others were frozen in place. In order to get the pins out the section had to be leveled. This was difficult to do because some of the floats were heavy with ice and water. Sledge hammers and bars were finally used successfully to remove the pins.
Each float was completely dismantled and then deflated. An officer of the 55th Treadway Bridge Company inspected each ponton and the unserviceable ones were burned. Except for the upstream anchor cable, the entire bridge was moved by 1800.
At 2300 hours, 3 January, Companies B and C received orders to begin the disassembly of the M4-M4A2 bridge on 4 January. The companies arrived at the bridge at 1600 to begin clearing ice from around the pontons, but the bridge disassembly did not begin until 1100, except for the removal of unnecessary cables, curbs, markers, and guide rails. A tactical development caused the delay. A British infantry-tank force was pocketed by the enemy north of Seoul and it was believed that a rescue force might be dispatched. This force did not materialize by 1100 and the dismantling was begun in earnest. The Eighth Army coordinator, stationed at the I Corps control point, set the time limit for dismantling at 1300. All equipment not removed at this time was to be destroyed. The I Corps engineer was able to get this extended to 1400, but at 1330 Eighth Army gave a standby order to blow the bridge, so all work halted. Half of the balk, the cables, curbs, markers, and guide rails were the only parts of the bridge salvaged.
Demolition materials were already at the bridge site. At 1100, unprimed charges were placed on the bridge while disassembly was going on. In general, the December plans for demolition were followed. Most important of the changes was the increase of TNT from 114 to 1,800 pounds, because of the shortage of tetrytol. The engineers used bangalore torpedoes to destroy the balk and, since they had no incendiary grenades, they substituted gasoline-soaked sandbags to fire the rubber pontons. At 1505 the firing order was received and the bridge was blown.
When the bridge did not sink after the first blast, a careful check was made. It was discovered that some of the charges had not fired. This was unusual. Ordinarily, sympathetic detonation will cause all charges to explode, and the failure probably was due to the explosives having become frozen. Inspection of the bridge proved it necessary to recharge and refire. After this was done the bridge was checked again. This time it was sinking. The end of the bridge was not spectacular, for the rapidly freezing water caused it to submerge slowly.
With the destruction of the M4-M4A2 bridge, all bridges across the Han River in the Seoul area were eliminated. It was a great disappointment to the engineers that they were not given time to disassemble this bridge, but all of the engineer missions in the withdrawal over the Han River were now accomplished.
5. End of the Line
Lt. Carrol W. Guth, 185th Engineer Combat Battalion. (Condensed from an interview by Lt. John Mewha, 8th Historical Detachment.)
The evacuation of Hungnam was not hurried, and each installation was demolished as soon as it was no longer needed. A railroad bridge and rolling stock were destroyed on 15 December 1950 by Company B, 185th Engineer Combat Battalion.
The 2,100-foot railroad bridge consisted of 29 spans, 8 of which were wooden-tie cribbings built up to the deck level. When Company B was ordered to destroy this bridge and all the rolling stock in the Hungnam area, it was decided that the projects should be linked. Spans of the railroad bridge would be destroyed individually and as many cars and engines as possible would be pushed into the void before blowing the next span.
About 15 engines and 275 cars were assembled for demolition. Korean railroad men helped shuttle the railroad cars from Hungnam to the bridge. When the Koreans learned that the rolling stock was to be destroyed they became reluctant-and had to be prodded to do the job. By contrast, the engineers found the job enjoyable-a release for their pentup emotions.
At 1545 the southernmost span was blown. Ten cars and several engines were pushed into the gap until it was filled. Some of the cars were loaded with gasoline and the engines had steam up. As they were pushed into the defile the wreckage caught fire. This process was repeated at each span. When the men reached the section of wood cribbing, several carloads of POL and an engine were spotted on top of it, and the cribbings ignited. The heat was so intense that the locomotive became cherry-red and its whistle started blowing. In a few minutes the whole section had crumbled.
As some of the cars were pushed into the gaps, the ends of the rails would spread and rip. This prevented other cars from being pushed off. Blocked spans were, therefore, blown with the rolling stock on them. By mistake, a boxcar loaded with demolitions was pushed onto some flaming wreckage. The resulting blast injured two men. The destruction continued throughout the night.
6. Destruction of Wonju
Lt. William H. Champion and MSgt. Julius R. Grupe, 2d Engineer Combat Battalion. (Interview by Lt. John Mewha, 8th Historical Detachment.)
The 2d Infantry Division was defending Wonju, but on 6 January 1951 it was again necessary to withdraw. To destroy communications through Wonju and to ruin those supplies that could not be evacuated, demolitions were ordered.
Although Wonju is divided by the Wonju River, it is linked by a railroad bridge and a highway bridge. North and east of the river was the 38th Infantry. It would be necessary for the regiment to withdraw across these bridges. For this reason the 38th Infantry was charged with their destruction. The actual demolition work was to be done by the 3d Platoon of Company C, 2d Engineer Combat Battalion. This narrative is primarily concerned with the actions of the 3d Platoon.
At this time the 3d platoon consisted of forty-two men and was commanded by Lt. William H. Champion. The platoon was in direct support of the 38th Infantry and had as its normal assignment the maintenance of the Chechon and Noto-ri roads.
During the evening of 6 January the 38th Infantry ordered the 3d Platoon to prepare to demolish the highway bridge, the railway bridge, 16 freight cars loaded with 80 tons of ammunition, and two tons of Korean rifles and ammunition located in a church west of Wonju. The demolitions were to be carried out on order of the commanding officer of the 38th Infantry.
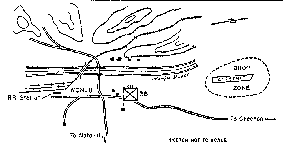
Wonju Area Map (12K)
The 3d Platoon was quartered on the second floor of a concrete building in Wonju which was also the CP of the 38th Infantry. At 0500 next morning, the men were awakened and told that an estimated three enemy battalions had infiltrated the regimental perimeter and were entering Wonju. Each man moved to his foxhole outside the CP building. The weather was a very cold 20 degrees, with snow on the ground and a sharp wind blowing. The platoon heard sporadic firing and occasionally saw tracers and flares.
At 0700, Lieutenant Champion and his four demolitions men prepared to go to the bridge sites. A jeep was loaded with explosives, and a driver was instructed to take a 3/4-ton truck loaded with demolition materials to the railroad bridge. Only 150 yards from the CP an enemy machine gun, located on high ground to the east, opened fire on the road. When the engineers saw the bullets hitting the road ahead, they concealed their jeep and took cover in a ditch. They soon saw a company of the 38th Infantry moving through town searching for the enemy. The company split, part of it moving toward the machine gun, which was silenced in five or ten minutes.
Lieutenant Champion and his demolitions crew walked with the infantry through Wonju, and the jeep load of explosives followed at a respectful distance. The infantry killed a number of enemy on its sweep through the village. They also set up a machine gun near the highway bridge and fired it at the houses east of the Wonju River. The engineers hand-carried their demolition charges to the bridge and worked under the covering fire of the machine gun.
The highway bridge was a reinforced concrete structure and the engineers had 450 pounds of Composition C3 with which to destroy it. Composition C3 is pliable and has great shattering power. It is much more easily used and will fit into places which cannot be reached by TNT. The engineers placed 200 pounds of the explosive on each of the first two piers, and 200 pounds on the deck of the bridge, to break it in the middle as the piers collapsed.
After fifteen minutes the friendly machine-gun crew departed and the demolition party was without security. To get observation, Lieutenant Champion moved northward in the river bed a few yards. Twenty minutes after he took up this new position the lieutenant noticed five or six North Koreans coming up the river bed single-file from the south. Evidently they were trying to get back to their own lines. The lieutenant shouted to his men. The lead enemy soldier, who had approached within forty feet of the bridge, reached into his blouse for a hand grenade instead of raising his rifle. Lieutenant Champion could not fire because his own men were between him and the target. One of the engineers shot this North Korean and the rest scattered behind a dike. Several more enemy soldiers joined the first group and a fire fight began. The engineers took cover behind the bridge piers and rocks in the river bed, but soon they flanked the dike and in fifteen minutes killed 9 North Koreans and took 3 prisoners.
After the fight ended, the men returned to the bridge and completed the placement of demolition charges. The engineers then moved to the railroad bridge.
The railroad bridge had nine or ten piers. The second and third were made of log cribbings, and the others were of concrete. As the railroad bridge was a stronger structure than the highway bridge, the demolition men used six hundred pounds of Composition C3 to mine it. They used 200 pounds on the first log-cribbed pier and 300 pounds on the first concrete pier. They placed 100 pounds on the top to breach the span. A five gallon can of gasoline was hidden in the log cribbing of the third pier for emergency use. Once the work was under way Lieutenant Champion drove off to the railroad station, leaving Sgt. Lester H. Johnson in charge.
At the railroad station Lieutenant Champion found sixteen boxcars loaded with ammunition of all types, scattered on three sidings. He decided that the best demolition plan was to wire the cars with primacord so the cars would explode simultaneously. As soon as his men joined him he assigned one man to set all the explosive caps while the others placed the demolition charges in the boxcars. The men placed a case of Composition C3 in each car on top of all the other explosives, and then set a detonator cap in a block of TNT on top of the C3. A complete circuit of primacord was placed around all the cars, with a connection run from each side of the primacord net through the boxcar into the case of C3. At the end of the net, four long pieces of primacord with fifty feet of time fuze (approximately twenty-five minutes' normal burning time) were extended to the vicinity of the railroad station. This was an added precaution in case some of the fuzes failed to burn.
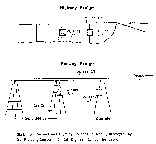
Sketch of Railroad and Highway Bridges in Wonju (15K)
It was 1030 when this wiring was completed. The demolition men returned to the CP building, and Lieutenant Champion drove up to the church building. When he arrived he found that the munitions were already prepared for demolition. After checking to see that everything was in order, he returned to the CP building.
While the demolition crew and Lieutenant Champion were away, the S3 of the 1st Battalion, 38th Infantry, ordered Msgt. Julius R. Grupe to take a squad to the airstrip to destroy the housing, gasoline, and other supplies in this area. Before leaving, Sergeant Grupe's men gathered all the tracer ammunition they could find. Then they marched through slush and snow to the airstrip, arriving both wet and cold. Airdrops had left some two hundred drums of gasoline, small-arms ammunition, and C rations scattered throughout the area. It was disheartening to the men to have to destroy so many supplies.
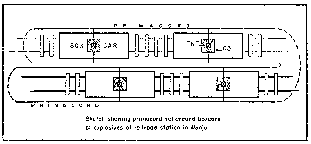
Sketch Showing Primacord Net Around Boxcars of Explosives of Railroad Station at Wonju (13 K)
One pair of men worked on each side of the field. Sergeant Grupe felt that two men would do a more effective job and that it would reduce the possibility of surprise. No effort was made to move the drums and the men fired tracer ammunition into them where they lay. The gasoline caught fire and burned down to the bullet hole, then exploded. Some twenty cases of small-arms ammunition were piled around one gasoline drum and set afire. It took ten minutes before the heat caused the ammunition to explode, and by this time the men had withdrawn to a safe distance. Ten to twelve cases of C rations were collected and given to the 38th Infantry. Three or four buildings which might have military use were fired with torches made of gasoline-dipped rags.
When the detail returned, it mined the CP building. At about 1730, the S3 of the 1st Battalion informed the engineers that the enemy had begun to infiltrate into Wonju again. Lieutenant Champion ordered his platoon, less Sergeant Johnson, to withdraw with the infantry CP group. The demolitions were to be blown at 1800, but when the hour approached the infantry had not cleared the bridges or the town. The authority to order the demolitions had been delegated to the commander of the 2d Battalion (Lt.Col. James H. Skelton).
At 1900 Colonel Skelton and his driver went to the bridges with Lieutenant Champion and Sergeant Johnson to make certain the area was clear. Colonel Skelton halted at the highway bridge while the two engineers drove up the river bed five hundred yards to the railroad bridge. Here they heard two or three enemy soldiers talking only ten yards beyond the bridge, near the point where the fuzes were located. The Americans dismounted and as quietly as possible moved to the third pier where the five gallons of gasoline were cached. Lieutenant Champion opened the can and poured it on the two log-cribbed piers. He and Sergeant Johnson threw matches into the gasoline and fired the bridge. Then they with drew-rapidly.
By 1920 the engineers were back at the highway bridge, but Colonel Skelton and his driver were gone. It was learned later that they had been forced to withdraw by the approach of enemy soldiers. A three-minute fuze had been stretched from thc demolition charges to a ditch on the Wonju side of the structure. As Sergeant Johnson approached the ditch a North Korean soldier jumped up and started to run. Johnson yelled and Lieutenant Champion shot this enemy soldier. The time fuze was pulled and the two men drove rapidly to the railroad station. On the way they heard the charges explode on the highway bridge.
The streets in Wonju were littered with rubble, and burning houses illuminated the area. No enemy was encountered. When the men arrived at the railroad station they ignited the time fuzes and stayed long enough to make sure the powder trains had started to burn. At the church they followed the same procedure.
All the fuzes lighted, the engineers drove south on the Noto-ri road. Within twenty minutes they had caught up with the infantry.
The powder train leading to the primacord net around the boxcars was old, and it took 1 hour 12 minutes to burn. At about 2100, when Lieutenant Champion was five or six miles south of Wonju, the sky lighted up and "it was light enough to read a newspaper."
When the Americans returned to Wonju it was found that all demolitions had exploded. The log cribbings on the railroad bridge had burned and the highway bridge had to be rebuilt. The boxcars were demolished and the CP and other buildings were completely gutted.
7. Mines Are Double-Edged Weapons
Lt. Sam D. Starobin, S2, 6Sth Engineer Combat Battalion
Mines are double-edged weapons. Properly employed they can be a strong instrument of defense. Improperly used they are a menace. Especially is this true for an army like ours, where vast numbers of trucks and tanks are employed. I have seen at least 150 disabled North Korean tanks -none of which had been destroyed by mines. I have also seen a great number of American tanks and trucks destroyed by our own mines. Not all of these were in minefields laid by Americans. A large percentage of the mines that destroyed our vehicles and killed our troops had been relaid by the enemy.
This need not have been so. We could have reaped a great advantage had we employed mines intelligently. American mine warfare doctrine is sound, but after Eighth Army had shipped 120,000 mines to units, only 20,000 were recorded or on hand. The remaining 100,000 were either abandoned or buried unrecorded!
The infantry sometimes asked my company to lay undefended minefields where there were gaps in their lines. The infantry commanders were advised that this was not a sound practice. But on several occasions these hard-pressed leaders insisted and we laid the fields. I know from personal experience that this often happened in other units.
The enemy found it easy to pick up the mines in unguarded fields and lay them behind our own lines. It was a convenient source of supply of the 20-pound mines for an enemy with a poor transportation system. When we did not cover our fields with fire we invited the enemy to mine our own rear areas.
A second method of losing mines to the enemy was by abandonment. Too many mines were moved forward. A change in the tide of battle resulted in the loss of large quantities of mines. Some commanders tried to destroy the mines, but this is not easy in the field.
Failure to record minefields was a serious problem in Korea. It is not until you return to a mined area that you appreciate accurate minefield reports. We should lay mines indiscriminately only if we never intend to return and do not value the friendship of the population. Yet we had repeated instances of units laying minefields which they did not record. Under the pressure of hasty withdrawal, mine-laying sometimes degenerated to pitching armed mines from the back of a moving truck.
When the 25th Infantry Division crossed the Han River in early March 1951, we started running into unrecorded American minefields. I personally visited units that had operated in the area and inquired about minefields. The S3 of the 3d Engineer Battalion recalled minefields laid by unit near Uijongbu which, under the stress of retreat, had not been recorded. A number of our vehicles had struck mines and soldiers had been killed at the positions he indicated.
As an engineer S2, I passed along to the infantry every minefield location that I learned of. I knew that long, technical reports would not be understood and that reports to the S2s did not reach the companies. I made large-scale sketches of minefields, using graphic symbols and non-technical language. These were duplicated and distributed down to the company commanders. When an infantry company commander saw that an attack would take him through a minefield, he called on the engineers to help him. The infantry respect those minefields now.
8. Learning by Doing
Major Richard I. Crawford, Korean Military Advisory Group. (Extract from a speech of 17 February 1951.)
The necessity for some type of land mine was becoming increasingly apparent as more and more enemy armor came in. At the outset we had no source of antitank mines; however, on Tuesday, 27 June 1950, we received word that General MacArthur's headquarters would support our efforts. We immediately asked for mines, and by Friday we had received about eight hundred.
The ROK troops had not had any training in antitank mines. In fact, they had never seen an M6 mine, but in this respect they had nothing on me. I had never seen one either. However, I had an advantage in that I read and understand English fairly well, and the instructions are pasted on the inside of the individual mine's carrying case. Shortly after the first mines were received, we instituted a short course on combat operations. We spent half an hour teaching the technique of laying and arming the M6 mines, and then we went off to the front.
As long as an American was closely supervising the operation, everything went fairly smoothly, but when the ROK engineers had to act independently we ran into trouble. Our half hour of training hadn't taken too well. They would forget to put the detonators in, or having done that, would forget to arm them. Their ideas of concealing the mines left much to be desired, and, on one occasion, one of my officers caught a detail on the road, just throwing the mines-carrying case and all-off the back end of a moving truck. It actually took the Korean engineers about two weeks before they laid any genuinely effective antitank minefields.
During this two-week period, the Koreans had "a better idea." Without our knowledge they prepared charges designed to strap around the waist of a soldier and formed some "body contact squads." Members of these squads were to move into the side of a tank, pull a fuze lighter on a two-second fuze, perhaps disable the tank, and certainly join their honored ancestors. I never found out how many tanks we actually disabled by this method, but I do know that in the first four or five days we ran awfully short of "body contact" people. The ROK Chief of Engineers told me he was experiencing some difficulty in getting additional volunteers.
Again, we ran into the ever-present problem of defending an obstacle. It required herculean efforts by the KMAG advisers to keep any force behind the minefields, and seldom were we successful until we got into our final defensive positions on the Naktong perimeter. The South Koreans were loath to use mines because of their previous mishandling. However, on the perimeter they did lay both antitank and antipersonnel mines. On one of the defended antipersonnel fields, we accounted for 113 enemy casualties in a two-hour night attack. This action raised the morale of our fighting forces, and at the same time created a supply problem: we couldn't get enough mines for them.
Later, on the road between Yongchon and Uisong, engineers placed a well-sited antitank minefield on the road and to each side of the road near a bridge. Again the field was defended. This time a tank came downhill, struck a mine, and turned sideways in the road. Another tank, following closely, tried to go around the first, and struck a mine. Our troops prevented any attempt to breach the field by laying down small-arms fire on the site, and a nearby tactical air control party called for an air strike. While the F-Sls were coming in, three more tanks and a selfpropelled gun came down the hill. The planes dropped napalm and rocketed all six of the vehicles. They claimed six kills on that operation. Not to be outdone, and on the theory that if it hadn't been for our engineers the Air Force wouldn't have had a target, we claimed six kills, too. Thus, some of the exaggerated reports we hear about.
9. Disregarding a Minefield
Major Glade S. Wittwer, S3, 8th Engineer Combat Battalion
While we were still in the Naktong perimeter, I saw an example of reckless disregard of elementary minefield precautions. The 8th Cavalry (1st Cavalry Division) was conducting local offensive operations three miles north of Chigol. One mile north of the town was a small stream. The existing bridge had a bypass already prepared to the east. Just beyond the bridge was an ROK battalion command post, and to the left was an 8th Cavalry aid station.
The North Koreans held ridge positions to the north. From these positions enemy infantry infiltrated on the stormy night of 17-18 September 1950. They had placed 26 U.S. M6 mines in the shoulder of the road and 18 in the bypass. Then the North Koreans placed demolition charges on the bridge and blew it thirty minutes before dawn.
All of this was done so quietly that one American sentry remained within a few feet of the minelayers without noticing them. The adjacent units were so surprised at the blowing of the bridge that they called the engineers to report that the bridge had been hit by a large-caliber shell.
Shortly after the bridge was blown, three M4 tanks came up the road. The first tank took the bypass and immediately hit a mine. Because the shoulder of the road was of loose sand, the mine blew off a tread but did not injure any of the crew.
The tank commander immediately detailed two crewmen to warn all traffic. Anticipating the arrival of a tank retriever, the second tank pulled off the road. It too lost a tread.
By now the rain had washed sand from above other mines and it appeared they were widespread. The tankers' warning was not enough for most Americans. Vehicles moved up into the danger area.
The next casualty was an artillery forward observer party. A lieutenant and his two radiomen drove up, were warned of mines, but still took the bypass. They hit a mine and all three were killed.
Soon an officer and an enlisted man approached in a jeep. The officer dismounted and the jeep went ahead. The driver decided that he couldn't make it. In turning around he hit two mines, and was killed.
This was the last attempt to use the bypass until the mines were cleared by an engineer detail, but vehicles continued to move up and stop on the shoulders of the road. One brigadier general pulled off the road and discovered that he had driven within twelve inches of becoming a statistic!
10. The Mine that Saved Sinnyong
Major David F. Campbell, Korean Military Advisory Group
From 30 August to 6 September 1950, the ROK 6th Engineer Combat Battalion engaged in unceasing mine warfare. All of its activities were in support of the ROK 6th Division in one of the most critical periods of the Naktong perimeter. If the battalion's success was greater than usual, it was because of the careful coordination of the mine warfare and the over-all tactics of the division.
The mountainous northeast sector of the Naktong perimeter was defended by Republic of Korea troops. In the center of ROK II Corps its 6th Division lay astride the Yongchon-Andong highway and the Kyonggyong South Line Railroad, with its command post at Sinnyong. In this area the highway and railroad run southeast to northwest, and are canalized by the mountains. Sinnyong served as the forward railhead for both the ROK 6th and 1st Divisions, with the main supply road of the 1st Division running through the sector of the 6th.
Opposing the 6th Division were the North Korean 1st, 8tb, 14th and 1stb Divisions, plus elements of an unidentified armored division. The enemy infantry was aggressive and applied continuous pressure. On the right flank the North Koreans occupied Hills 783 and 828, seriously threatening Sinnyong. The 6th Division had to remain on the defensive in the center and left in order to take the offensive on the right to protect the communications line. The division's front was extremely broad because its line was curved. Shrewd use of mines allowed the division to straighten its line and shift a maximum number of troops to the offensive.
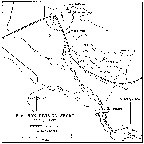
6th ROK Division Front: 30 August 1950 (18K)
Not only was there infantry pressure, but from the main highway North Korean tanks lobbed harassing shells into Sinnyong. The fire was unobserved and most of the rounds landed in the rice paddies, but small deflection shifts would have scored hits on the MSR, the marshaling yards, and military installations.
A staff conference was called on 30 August to consider ways to stop this tank menace. The division commander (Major General Kim), his KMAG adviser (Lt. Col. Martin 0. Sorenson), the division engineer (Major Pak), and I were there. It was decided that the engineers would be responsible for stopping the tank fire, but any action we took must fit into the larger division defense plan.
The enemy tanks approaching Sinnyong came down the highway from Yodok-tong to a curve in the road. A crater in the road, a small minefield, and a platoon of engineers prevented them from rolling on into Sinnyong. No additional troops could be spared from the division to reinforce the position. Fortunately, the tanks could not flank our position as the road was winding and narrow and there were sheer drops of three hundred feet from its edge. Although the enemy had not tried to force the roadblock, we decided that the position must be strengthened.
That evening the corps engineer (Col. Lew Won Sik), his KMAG adviser, two KMAG advisers from the ROK 19th Infantry (in whose section the roadblock lay), Major Pak, I, and our interpreters made a reconnaissance. At the roadblock we picked up the platoon leader and two engineers. We moved 250 yards beyond our forward positions to the road crater. It was not quite dark, so we could look directly into Yodok-tong and the enemy front lines. As dusk approached we could see the North Korean infantry crawl out of their hiding places in the town and mill around.
We decided that the terrain and the steep wall flanking the road made this an ideal tank trap. We could station a bazooka team at the crater, have infiltrators mine the road near Hwasu-dong, and send tankhunter teams along the road.
After thirty minutes at the crater we began receiving sporadic artillery fire. We returned to the division CP in Sinnyong and there continued planning our tank trap, mine program, and demolition of a railroad tunnel. Generally, the minefields were to be heaviest in the center. To undertake the minefield program I requested and received two platoons of engineers that were being used as infantry.
Later in the night the engineers emplaced forty M6 antipersonnel mines over sixty yards of the road at the point where the tanks stopped to fire (Minefield 1). Unlike our previous laying of M6 mines, these were not only armed but each was activated by placing an M3 antipersonnel mine underneath it, and then attaching a three-inch trip wire to the handle.1 We made this field even more formidable by placing fiftytwo antipersonnel mines along the narrow shoulders of the road with trip wires laced across the road and its shoulders. This would take advantage of the practice of the North Koreans of surrounding their tanks with engineers to clear mines and infantry to prevent close-in attack. Since the tanks would be canalized by the twelve-foot road, we figured that our preparations would be effective against infantry-armor attack. Fortunately, no enemy tanks arrived to interrupt our work.
While this minefield was being constructed Minefield 2 was being installed nearby and tied in with Minefield 1. About 250 M3 antipersonnel mines were laid south of Yodak-tong in an inverted chevron pattern. We worked quietly, and the enemy all around us did not recognize that we were ROK troops.
On 31 August the sketches of our previous night's activities were recorded and sent forward. A great deal of time was spent in making a physical inspection of all existing minefields and making plans for strengthening them.
Arming a mine is the process of removing all safety devices. Activating a mine is the process of booby-trapping it, either by setting an internal fuze or by using another mine.
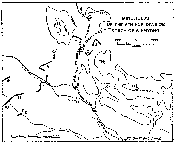
Minefields of the 6th ROK Division North of Sinnyong (19K)
On the night of 31 August-1 September, Company A, ROK 9th Engineer Combat Battalion, laid ninety M3 antipersonnel mines in an extension of Minefield 2 (Minefield 3). These made a second chevron. In using the chevron pattern we were following the Soviet system, which the North Koreans employed. It was not only the efficiency of this pattern that attracted me but its deception, since the North Koreans would not expect it.
We completed our work at about 0200, and the minefield party began to withdraw. We were careful to go east of the field, to take advantage of the protection of the field itself. Just at that moment a company of North Korean infantry began an attack. They came from the direction of Yodek-tong, bunched up and running upright. Almost the entire company got into the first belt of mines before they hit the first trip wire and realized their predicament. Mines exploded and men screamed. The attackers turned in panic only to kick more of the trip wires. The whole affair lasted scarcely five minutes, yet we estimated a hundred casualties. We returned to find our minefield badly damaged. Artillery fire began falling, so we left without making the repairs. As the result of this experience I tried thereafter to get infantry protection for minelayers.
I spent a good part of the next day (1 September) teaching expedients for overcoming the shortage of activating devices, and devoted some time to instruction in booby traps. The South Koreans were especially interested in booby-trapping the little carts the enemy used to carry supplies, so I devised a method. An infiltrating party would remove a wheel, place the axle on the ground, and fasten a trip wire to the axle. When a group lifted the cart to replace the wheel the booby trap went off. This diabolical device was referred to by the ROKs as "the shaver" -from the effect it had on one's head. Teams went deep into the enemy lines and placed numerous booby traps, all of which were carefully recorded.
The same day we began to activate antitank mines. Except for Minefield 1, this had not been done before. In fields over 500 yards long, we activated 20 per cent of the mines. The smaller fields we activated 100 per cent.
That night (1-2 September) we laid two more minefields. One of these, Minefield 4, was placed to the rear of Yodok-tong to form a part of our tank trap-when we should get around to springing it. It consisted of ninety antipersonnel mines, with trip wires, laid over an area of nine hundred yards. The other field was to the left of our roadblock on the main highway. The need for more troops on the right flank of the division was so strong that even the engineer platoon at the roadblock had to be redeployed.
During the night of 2-3 September we continued with our minelaying and completed two more fields. Just before these fields were completed, the infantry on the left flank of the division was pulled behind the minefields and the gaps left for the purpose were closed. We continued to strengthen our old fields, and even repaired Minefield 2, where the attack had occurred. The enemy dead remained as a warning to others who might attempt to attack at this point.
Now that we had minefields across the division's front and had readjusted our lines' we were ready to spring the tank trap. On the night of 3-4 September we formed two engineer and one infantry 3.5-inch rocket teams. At 1900 we moved out to the crater and left Team Able (four engineers) with instructions not to fire until they heard firing from one of the other teams. Two hundred yards farther north on the road we left Team Baker from the 19th Infantry, with instructions to lay low until they heard fire from the northern end of the trap.
The third bazooka team accompanied a platoon of engineers, which I led, to the bridge at Hwasu-dong. We moved around to the left of Minefield 4, kept quiet, stayed in defilade, and were able to move into enemy territory without causing alarm. We found that the bridge at Hwasu-dong had been damaged by the Air Force, but that the enemy had made a ford fifty yards northeast of the bridge.
North of the bridge we laid a hasty minefield from the river to the ford. Moonlight made the work easy and flashes of distant artillery increased the visibility. The rocket team selected a position two hundred yards south of the bridge and some fifty yards off the road. The engineers joined them, and all began to dig shallow foxholes. As we heard our artillery plaster the enemy, we were glad we had coordinated our movement before coming into the area.
At midnight, about forty-five minutes after we had taken up positions, we heard tanks coming down the road. These were preceded by a mine-clearing team, which easily found the mines on the top of the road. We saw the lead men drop to their knees, grab the mines without examining them, and throw them off to the shoulder. None of these mines exploded for they had not been activated. But we could see from the careless way their engineers handled the mines that they were in for a surprise!
As soon as the tanks had breached the minefield they forded the river and moved on with their foot party. I don't know how many tanks passed, but by the artillery flashes I counted five T34s. When no other tanks passed our position for twenty minutes, I sent two squads of engineers to place a deliberate minefield in the road, each mine of which was to be activated. After this was done, I knew we had the tanks.
Just as our mine squads returned to our positions, a lone enemy tank came down the road without foot troops accompanying it. I guessed it was from the same party as the first tanks, but had fallen behind. The tank approached the end of the bridge and stopped. One crewman had started to get out of the tank when our bazooka team edged up to within fifty yards and fired. The projectile struck just behind the turret. None of the crew escaped and the tank burned, blocking the road. The ROK troops became excited for a few minutes and fired their rifles to catch anyone in the vicinity. Then we withdrew quickly to our own lines. We soon heard a great deal of firing to the south, which meant that our other teams were in action.
Team Able was seventy-five feet above the road where the first tank would have to halt. It remained quiet and allowed the first tank and accompanying party to approach. Ten or fifteen enemy engineers moved along the road on their hands and knees, feeling for mines. When they reached the first activated mine and felt its pressure plate they jerked it out! The explosion killed every one of these men.
The infantry, as we had anticipated, rushed for the shoulders of the road, and immediately ran into our maze of trip wires on the antipersonnel mines. Of the 50 to 100 men, surely half were killed.
Until now neither bazooka team had fired. Five tanks had passed Team Baker but the team waited to see if there were more. By the time they knew that this was all, the last tank was masked from their fire. The rocket team moved to the road. As these men rounded the bend, the rear of the fifth tank was only fifteen to twenty yards away. The gunner heard the exploding mine and he fired directly at the tank. This tank exploded and burned, blocking the road. The bazooka men scurried up the bank and headed for home.
Within a minute of these two actions, Team Able fired down on the first tank and hit it at the junction of the turret and the motor. The force of this explosion ripped off the turret and the ammunition blew all at once. The second explosion lifted the tank off the road and hurled it down the steep bank three hundred feet into a rice paddy, where it landed upside down. As Team Able was not in a position to fire at any of the other tanks, it headed for our lines.
During the night I sent bazooka teams along that road and two more tanks were destroyed. One was destroyed by the infantry and there was a squabble between the infantry and engineers for credit for the second. The argument was heated, for the Republic of Korea offered a bonus of a hundred thousand won to each unit that destroyed a tank.
During the night we had destroyed five T34 tanks. In the morning Colonel Sorenson sent an air reconnaissance party forward and they called for Mosquitoes to sweep the area. These planes found nine more tanks in our trap. Air strikes destroyed all nine.
Our tank party over, there were other problems. Pressure in the north was growing and we had to move more troops to the right flank. A captured tank lieutenant told us the enemy had brought eighty-five tanks into our sector on 1 September. We knew that our bag of fourteen had hurt them, but we didn't think our present positions would hold against a heavy thrust. We began cratering the main highway and laying additional belts of mines behind a straighter front line. We also turned our attention to blocking the railroad tunnel.
Our tunnel project had waited while we collected TNT. At the east end of the tunnel we now placed 2,350 pounds of TNT pressure charge in the overburden so as to completely close the tunnel's mouth. At the west end we placed only 900 pounds. We did not place enough TNT in this end of the tunnel to completely block it since we hoped to lure the enemy into the entrance. Then we placed fifty-two booby traps with trip wires. The preparation was completed on 5 September, but the charge was not blown until the next day.
On 5 September the enemy began a drive on the front of the ROK 8th Division (on our right) and by 9 or 10 September had taken Yongchon, some ten miles to our rear. The 19th Infantry was placed to protect our rear. Once more we had to shorten our line, and it was minefields that gave us time to move and erect a defensive barrier. Not only did we build up our own defenses; we also took the mines to the enemy, infiltrating ten miles deep and placing mines and booby traps as far back as Habon-dong.
On 6 September we blew the railroad tunnel. After this we entered the west opening and completed our job of boobytrapping it. The ROK 2d Infantry was drawing back at this time. As these men moved over the mountain which the tunnel cut through, the enemy tried to use the tunnel to cut them off. The first men ran into the booby traps and some six or seven were killed. The pursuing party withdrew and started to move northeast in hopes of taking RJ 775928 and blocking the troops withdrawing south along the main highway. They ran into Minefield 8 from the south and here lost ten or fifteen more men. The group then withdrew to the northeast in confusion and did not further interfere.
As our infantry withdrew down the Yodok-tong road toward Hill 728, the enemy attacked banzai style and a regiment strong, through Minefields 2 and 3. These minefields had been built up to contain some five hundred antipersonnel mines, and we had them covered with small arms fire. Rifle and machine-gun fire did not stop the enemy, but the mines stopped them cold. They milled around for a few moments trying to find a passage, and the automatic weapons and mines wounded or killed five hundred. The attack soon stopped and our men withdrew without further interference.
After this engagement and the shortening of our line, we continued cratering the roads and increasing our mines. The ROKs thereafter had great faith in minefields, learning particularly that minefields supplement other means of defense.
11. Recon Dailey
MSgt. Warren F. Dailey, Sgt. Earl J. Cayemberg, and Cpl. Elmer L. Bartley, 2d Engineer Combat Battalion. (Interview by Lt. John Mewha, 8th Historical Detachment.)
The amount of timely engineer support that can be given to the infantry squads depends greatly on the speed of the engineer reconnaissance. During the operations of the 2d Infantry Division along the Soyang River in the first week of April 1951, the 2d Engineer Combat Battalion kept a number of aggressive engineer reconnaissance teams searching for new access roads through the mountains and for obstacles requiring engineer clearing.
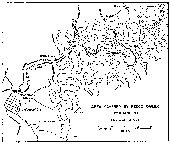
Area Covered by Recon Dailey (22K)
Two of these engineer reconnaissance teams were commanded by MSgt. Warren F. Dailey and Sgt. James G. Sulzer. Sergeant Dailey's assistants were Sgt. Earl J. Cayemberg (radio operator) and Cpl. Elmer L. Bartley (driver). The teams moved out from the engineer battalion at Samsong-dong on the morning of 2 April and headed toward Chunchon. On the way they reconnoitered two lateral roads, which had been constructed by the Marines, to see if there was any way to continue the roads across the mountains. There was not.
The teams reached Chunchon at 1530 and reconnoitered several roads to the east. (1) The roads soon dwindled into trails. That night the two teams stayed with the 8th Engineer Combat Battalion (1st Cavalry Division).
At 0715, 3 April, the teams investigated roads east of Chunchon and south of the Soyang River. (2) At Chamjan-ni the teams split, and Sulzer headed north to the river to look for a ford. He found the river was too swift and deep. Sergeant Dailey covered the roads to the east and southeast, only to find they ended in trails against the sharp hills.
At 1200 the teams rendezvoused (2) and were joined by Lt. Henry P. Leighton, who came to receive their report. He told them to recheck the first two roads. A power line crossed the mountains and the battalion commander hoped it would be paralleled by a usable trail. In any case, the teams were to remain in the Chunchon area and attach themselves to Company B as soon as it arrived. The teams were then to reconnoiter the main supply route leading east from Chunchon to Yanggu.
The teams rechecked the roads. An investigation of the power line disclosed that the towers had probably been packed into the mountains on mules. Not even a jeep could follow the rough trail. The teams checked other roads on foot, and then returned to Chunchon for the night.
On 4 April, the two teams took note of roads and bridges through Chunchon. The sixteen-span bridge over the Soyang River had been blown. The teams crossed on an improvised bridge built by the 8th Engineers and continued their reconnaissance eastward until they came to a minefield that had destroyed a tank and a truck. Following a temporary bypass around the minefield, the teams continued driving along the road between columns of men of the 23d Infantry.
By 1530 the teams reached the edge of a huge, hand-dug crater- 20 feet long and 30 feet deep. The high ground northeast of the crater was still in enemy hands and the infantry were fighting in the hills, especially on Hill 568. Sulzer and Dailey walked with the infantry along the road and found a great number of obstacles. There were antipersonnel mines, wooden box mines, felled trees, and rubble blown onto the road.
Near a small bridge an enemy machine gun opened fire and hit three infantrymen. The infantry started to withdraw. The engineers ran back along the road until they were masked from the fire, and then walked carefully along. Several times they saw suspicious holes in the road and by probing with their carbine bayonets the men would feel the mine cases. Sergeant Dailey removed detonator caps from two.
At their jeeps the engineers wrote up their reconnaissance report, but as they could not make contact with battalion by radio, they called Company B. The company commander informed them that he had a message for them.
When the teams reached the Company B command post east of Chunchon, the company commander relayed the order that Sergeant Sulzer was to return to the battalion command post with maps and reports of the past three days. At 2200 Dailey received a message to continue the reconnaissance.
Next morning Dailey and his men returned to the crater. The 8th Engineers had made some temporary repairs and a jeep could cross it- with difficulty. There was evidence of road mines, and one destroyed trailer showed their effectiveness.
An infantry officer told Sergeant Dailey that "French Road" was heavily mined, so Dailey and Corporal Bartley dismounted before inspecting it. They found mines-and mangled bodies. Some mortar rounds were fired at the engineers, and they turned back, their pace increasing when small-arms fire kicked up dust at their feet. Heavy fighting continued on Hill 568, and six air strikes hit the crest.
By 0900 the team was driving ease along the main road. The Antitank and Mine Platoon of the 23d Infantry was sweeping the road for mines and blasting trees and boulders out of the road. Some distance forward, the team met Lt. Russell 0. Blosser with another reconnaissance party from the 2d Engineer Battalion. The lieutenant's jeep had a flat tire. While repairs were under way a mortar concentration struck near by. The engineers took cover in a ditch but later, when they had repaired the tire, moved the vehicles back out of sight. Lieutenant glosser and Sergeant Bailey moved eastward on foot.
At a defile in the road the engineers met infantry observers and several tanks. Artillery rounds struck near the tanks, and the engineers had to duck as best they could. Forward of the defile the road was cratered. Lieutenant glosser instructed Sergeant Dailey to return to the jeeps and radio Company B to send forward a D7 bulldozer, four truckloads of sandbags, and a platoon of engineers. The message was sent, the work done, and that afternoon traflic continued along the road.
In the afternoon Sergeant Dailey and Corporal Bartley moved beyond the defile to within three hundred yards of the enemy-held village of Naepyong-ni, and then worked northward on a small trail to Hachon. Much of this reconnaissance was through enemy territory. Minefields and trail conditions were recorded.
Recon Dailey (Dailey, Cayomberg, and Bartley) continued to operate with or ahead of the infantry for four more days before they were relieved. Their operation was typical. Their results were speedy support by the engineers and rapid advance by the infantry.
3. Inexpedient Expedients
Lt. Norman R. Rosen, 10th Engineer Combat Battalion
Field expedients are essential to combat engineer operations, especially when supplies are critical as they were in Korea. But some units disregarded sound military engineering principles in their use of expedients. When an engineer replaces a bridge with a twelve-inch culvert and uses rubble fill, this isn't expediency-it's ignorance.
In February 1951 the 3d Infantry Division was advancing toward the Han River. The railhead for the division was to be moved up from Suwon to Anyang-ni. This move would reduce the truck haul of division supplies by twenty miles. To make the shift possible, Company D, 10th Engineer Combat Battalion, was given the mission of opening the road.
At one point we lost time because someone had used an "expedient." A twelve-foot concrete bridge had been dropped, probably in the summer of 1950. Later the road was opened again. The stream was a small trickle during some seasons, a swift-flowing body of water during others. When the concrete deck of the bridge fell it left a three- or four-inch opening. The working party that opened the road made no repairs, but filled the void with rubble and trash. This was adequate at the time, since the winter of l9S0 was dry, but with the rains coming in the spring of 1951 we knew we had to build a better structure.
When we started to remove the fill from the hole we ran into real difficulty. The space between the abutments was too narrow to use a bulldozer. Besides, there was limited traffic on the road and we had to keep it open. This forced us to clear the stream bed by hand.
If the fill in this case had been gravel or rock it wouldn't have been so bad, but we had to extract an ox cart, sand and rice bags, corn stalks, straw mats, and other items. All of these had become wedged and frozen in place. We had to use a full squad of men for a day and a half to clear the rubble. Each half of the bridge took less than four hours to build. In this job, like many others, the clearing of the site on which an expedient had been used took more time than the building of a new structure.
13. The Delay at K-2
Major Walter C. Henderson, 822d Engineer Aviation Battalion
The 822d Engineer Aviation Battalion was located on Okinawa in July 1950. We were special-category troops assigned to the Twentieth Air Force. Early in July we received orders from Headquarters, Far East Air Force, placing us on temporary duty with Fifth Air Force in Korea. It was intimated that we would be away only sixty days, and we were told we could leave our families, footlockers, and winter clothing on Okinawa until we returned.
When I returned to the United States in August 1951, the 822d was still in Korea. During all of these fourteen months the 822d had had all or part of its forces at the K-2 airstrip near Taegu. We had, however, received so many changes of plans that much of our time was wasted.
On 5 July 1950, the battalion commander (Lt.Col. Frank J. Polich) and I flew to Tokyo to the headquarters of Far East Air Force. Here we were oriented by the director of installations, and we submitted reports on the status of our battalion and requisitioned equipment. We explained that half of our personnel were due to return to the United States immediately, either on completion of their overseas tours, or for discharge. Later regulations issued by the Department of Defense prevented this exodus from taking place but left us with a serious morale problem.
On 8 July Colonel Polich and I accompanied the directors of installations of Far East Air Force and Fifth Air Force to the K-2 airstrip. This was the final reconnaissance for the Tokyo officers, a preliminary one for us. Colonel Polich and I retrained at the field when the others left, so that we could continue our inspection and begin our planning.
Our first view of K-2 showed us an old Japanese sod-and-gravel runway, its surface scarred with pot holes. The strip was 300 feet wide and 3,800 feet long. Our job was to repair it so it could handle "moderate traffic for a minimum time." After the repairs were complete we were to lengthen the runways to 5,000 feet so that our combat planes could use the field.
Our instructions stated that the work would have to proceed without halting the air traffic. This made our job more difficult. We divided the strip to make two runways. The one closest to the control tower was designated A, and the far one B.
Work began on 18 July. Dust and the psychological effect of the wing tips were our earliest problems. We regraded the crown and hauled fill on Strip A so that eventually the center of this strip was eighteen inches above its former level. Near the west end of the old runways, we encountered "Air Force blue" clay-the soft silt that makes up the rice paddies. A truck could run over it once, but repeated trips would break through the thin crust and no bottom could be found. Of course, this would not carry a heavy plane. To strengthen the strip we excavated five to ten feet, and filled the pit with crushed rock. This made the end of the runway an island of gravel in a sea of soft clay.
We had our renovation completed and the pierced-steel planking laid on Strip A by 7 August. We opened Strip A to traffic and closed Strip B. On this second runway we intended not only to renovate but also to lengthen it to five thousand feet. When we finished Strip B we expected to lengthen Strip A.
Remembering the soil conditions we had encountered in Strip A, we decided to build the extension above the ground on a base of crushedrock fill. Although this caused a slight grade increase, it would not raise any problems as long as the runway did not exceed six thousand feet. We didn't anticipate the airstrip going beyond that distance because of the natural obstacles at each end.
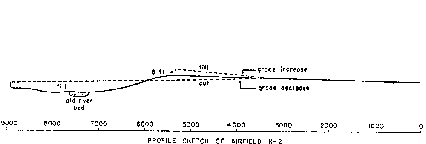
Profile Sketch of Airfield K-2 (4K)
Before we had lengthened Strip B to five thousand feet, the tactical situation forced us to evacuate the battalion to Pusan. Here we began the K-9 strip and, as time moved on, we began to suspect our stay in Korea would not be limited to sixty days.
When the tactical situation at Taegu improved we moved Able Company back to the K-2 strip. Shortly thereafter they had to evacuate again, and on their second return to Taegu they were ambushed by
North Korean guerrillas. Able Company remained detached from the battalion and continued at K-2 while we went north to Pyongyang and then made the retreat. By February 1951, the full battalion was againassembled and working at K-2.
Under changed specifications Able Company had lengthened both runways to 5,700 feet, and then remained at the field working on the overrun. But now we received new specifications requiring us to lengthen the runways to 9,000 feet with 1,000-foot overruns at each end. K-2 was to become a jet-fighter field.
An airstrip of this length may seem unusual for fighter aircraft, but jets make this and other improvements necessary. Jets do not have the rapid take-off and climb of propeller-driven aircraft, especially in the combat zone, where they are heavily loaded. The runways have to be strong and smooth since jets have very narrow tires which are inflated up to 190 pounds. The narrowness of the tires gives a very high weight per square inch on the ground and calls for a strong surface. Smoothness is necessary because of vulnerability of high-pressure tires, and the high landing speeds (often more than two hundred miles an hour) of jets. Another important factor is the sensitivity of jets to dust
All of these factors make the jet airstrip ideally one with an asphalt surface covered by pierced-steel planking. Yet even this surface has its difficulties. Some jet models lose a good deal of fuel on take-off, and this fuel has a corrosive action on asphalt. Tail blast and heat from later models cause the surfacing to deteriorate.
When we got out new specifications to push the runways of K-2 to nine thousand feet, we ran into two types of problems. The first were those imposed by Nature; the second, those arising from the piecemeal planning.
To the east of our runways was a hill mass which already presented a dangerous glide obstacle. To extend the field in that direction was out of the question. Going west we encountered a village and a river. We dug a new bed for the river, looping it about two miles around the end of the field and overrun. We had to demolish the village.
The piecemeal planning problem gave us the most trouble. In August we had raised our grade level at the 3,800-foot mark to overcome the unstable soil conditions. Now we were going to have to lower the grade level so we could cross the old stream bed without placing an uneconomical amount of fill. Fortunately, the drainage ditches we had dug to the north of the strip had stopped the underground water from reaching the former rice paddies that were now our airstrip. The soil was now more stable, but we had to go back to the 3,800-foot mark, take out all our original fill, and start excavating below the old ground level. Our former runway extension work was not only a complete loss, but we also lost additional time taking out the fill we had hauled in.
By the time I left Korea the runway jobs had progressed to the point where the surfacing was to be applied. The asphalt was planned to be three and a half inches deep, and the pierced-steel planking to cover it was already stored in piles on each side of the runway. At this time, however, specifications were again changed to make the asphalt six inches deep and to apply the pierced-steel planking only to the last five hundred feet of the runway. When you consider that the 1,200,000 square feet of pierced steel planking that was not to be used at this site is both heavy and bulky, you can imagine the tremendous waste of manpower and transportation that was involved.
The building of K-2 took more than a year. Admittedly it was a big job and would have taken a lot of time and effort under ideal conditions. But the constant changes of plans led us to fill where later we were to dig, and haul pierced-steel planking to places where we were going to use only asphalt. Such changes made K-2 agonizingly slow and expensive. It also meant that jets could not come to K-2 when they were first needed. If the high-level planners had anticipated the final product, our project would have developed differently.
14. Equipment Without Operators
Capt. James E. McClure, Heavy Equipment Maintenance and Repair Officer, 76th Engineer Construction Battalion
The 76th Engineer Construction Battalion was on Okinawa when we were alerted to move to Korea. All weak equipment was exchanged and only the most aggressive officers and best-trained men were taken with the unit. In Korea we made a splendid record, but there were some occurrences that we are prone to forget.
From the moment our advance party arrived in Korea, the battalion was given an overload of work. To complete our missions we overworked our men and equipment. I shall not concern myself with the loss of morale and efficiency resulting from the long hours of work, or from assigning men the maintenance responsibility for three or more pieces of heavy equipment. I will only tell how the overload affected the equipment.
In August 1950 Ammunition Supply Point No. 1, near Pusan, had to be relocated to allow the construction of an Air Force runway. The area chosen for the new ASP was in the mountains two miles from the unloading piers. Ammunition bunkers were needed immediately since seven ammunition ships lay at anchor waiting to unload their cargos.
The engineering officer of Pusan Logistical Command assigned the construction of the ammunition bunkers to the 76th. He told our battalion commander (Lt.Col. Thomas K. Fullerton) that twelve additional D7 crawler tractors were available at the engineer depot and must be drawn to increase the battalion's work capacity. He ordered a 20hour schedule until enough bunkers were completed to unload the anchored ships.
A battalion staff conference followed. During the discussion I pointed out that no surplus of trained equipment operators existed, and that the additional tractors would impose a hardship on the battalion without notably increasing production. Without trained operators there would be no preventive maintenance, and without that the tractors would not operate very long. In spite of these arguments, the directive to the battalion was specific and the colonel had no option but to order: "We will have to utilize the cooks and company clerks, if necessary, for operation of the additional equipment."
As equipment operators we selected carpenters and other men who had mechanical skills, and held a class on operation and preventive maintenance. We could only hope that the men would learn enough to get them by. Then the twelve D7 tractors were dispatched to the project site, and three qualified mechanics accompanied the group to support the operation.
After one day's operation the mechanics were swamped with deadlined tractors. The power-control units were all going bad, the grease seals were blowing, and the operating bands were overheating. There was no great showing of completed ammunition bunkers after forty-eight hours of continuous operation. In addition, half the tractors were out of action. The intense pressure from above to complete the project continued. Another battalion staff conference was held and it was decided to work two ten-hour shifts daily, and devote two hours of each shift to instruction and preventive maintenance. This prevented some tractors from deadlining. The work continued slowly but we kept ahead of the ammunition people because they had serious difficulties in their own operation.
On 25 August, Pusan Logistical Command again assigned us a new project with top priority. This was to build a POW inclosure, which involved draining a rice paddy and eliminating its lower areas with ten thousand cubic yards of fill. Unfortunately, the nearest fill obtainable had to be hauled five miles from a burrow pit.
Another meeting of the battalion staff was called to discuss the method of starting this project at a time when all of our battalion's personnel and dump trucks were otherwise engaged. Since we already had eight to ten top-priority projects assigned us, there was no reason to halt one to advance another. Additional dump trucks were available in the ordnance depot but again we had no drivers.
After much discussion, Colonel Fullerton accepted a tentative plan. Forty-three dump trucks would be drawn from the ordnance depot, and Korean civilian personnel would be trained as drivers. These trucks would be divided into two platoons, each to be controlled by a U.S. enlisted man with dump-truck experience. All Korean drivers would be kept in convoy with the enlisted supervisor driving the lead truck and controlling the speed. Finally, motor stables would be held daily, with the supervisor calling out each preventive maintenance point to be checked. Korean interpreters would relay the instructions to the drivers. This would insure daily preventive maintenance service on the Korean operated equipment.
This plan was approved and put into operation. It worked very well for two months, with eighty per cent of the dump trucks serviceable and dispatched. Some time was lost at the excavator while waiting to load, but the control which the convoy plan gave us appeared to me to justify the loss of time. Colonel Fullerton, the S3, and I held several conferences concerning the time lost, but all agreed it was necessary to follow the original plan.
In October I had to be gone for two days. When I returned I found a new plan was in operation. Now, each Korean driver was individually responsible for his truck, and there was no immediate control by the enlisted supervisors. Trucks moved independently and the supervisors had little control over the forty-three trucks.
Three weeks after the initiation of this new policy, half the dump trucks were deadlined. These repairs often were necessary because the Koreans had not performed any preventive maintenance. The trucks, moving independently, were driven at excessive speeds and there was a high toll of broken springs and blown-out tires. The Korean drivers visited their homes for hours, and even sold their gasoline. Few of the drivers seemed to have any sense of responsibility.
As the efficiency of the operation declined rapidly and the number of deadlined trucks rose, the S3 came to me to complain about the trucks not operating.
I replied that the original policy of supervised operation and maintenance should be immediately re-established.
The operations officer, thinking only of immediate progress, answered: "It can't be done. We lose too much time that way."
I asked: "What are you accomplishing by your present policy?"
The S3 retorted: "You're the maintenance officer. It's up to you to keep the trucks rolling."
Causes of the Korean Tragedy ... Failure of Leadership, Intelligence and Preparation